在實際的生產(chǎn)過程和其他運動體控制過程中,被控對象所要求的運動形式通常有兩類:一類是被控對象本身做旋轉(zhuǎn)運動,如圖1—4a所示;另一類是做有限長度的直線位移運動,如圖1—4b所示。
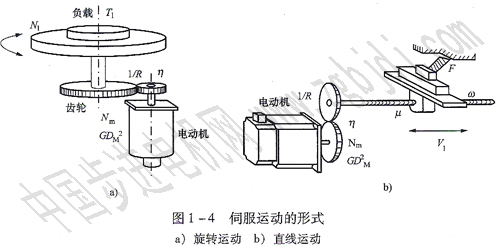 在過去相當(dāng)長的時期內(nèi),這兩種機械運動都用旋轉(zhuǎn)伺服電動機驅(qū)動。對旋轉(zhuǎn)運動的機械負(fù)載(如,立式平面磨床的旋轉(zhuǎn)工作臺),自然可以采用旋轉(zhuǎn)伺服電動機驅(qū)動,為了獲得適宜的力矩和速度,在兩者之間只需加設(shè)減速器,不必做運動形式的變換。如果為省去減速器,則可以采用直接驅(qū)動方式。 實際上,在生產(chǎn)中存在著大量的直線運動機械,如圖1—4b所示,機床各坐標(biāo)軸的伺服控制就是典型的例子。在采用旋轉(zhuǎn)伺服電動機驅(qū)動時,要想再控制運動對象在終端實現(xiàn)直線位移運動,就必須設(shè)有將旋轉(zhuǎn)運動轉(zhuǎn)換成直線運動的變換機構(gòu)。在精密進給伺服控制時,機床上一般都采用滾珠絲杠等機構(gòu),如圖l一4b所示。有些情況下,電動機輸出軸端也可能加裝減速器。對直線運動的機械系統(tǒng)來說,應(yīng)該了解機械傳動鏈上的各部分參數(shù):電動機的轉(zhuǎn)動慣量Jm(kg·m·s的平方)電動機轉(zhuǎn) 速Nm(r/min).機械傳動效率η,減速比l/R,滾珠絲杠的螺距P(mul/r),絲杠與工作臺之間可動部分的摩擦系數(shù)μ,工作臺的質(zhì)量M(kg),切削力F(N),工作臺運動速度V1(m/min)等。對旋轉(zhuǎn)機械系統(tǒng),參數(shù)還包括負(fù)載的轉(zhuǎn)速N1(r/min)和負(fù)載軸端的轉(zhuǎn)矩T1(kg·m)等。 既然在機床進給伺服驅(qū)動中,由旋轉(zhuǎn)伺服電動機通過滾珠絲杠帶動刀架和刀具獲得最終的直線運動,那么能否直接采用直線驅(qū)動,省去中間的滾珠絲杠等機械運動形式變換環(huán)節(jié)而獲得終端的直線運動呢?實踐證明可以,而且也是勢在必行。近些年來,由于加工技術(shù)要求質(zhì)量和效率很高,傳統(tǒng)應(yīng)用的“旋轉(zhuǎn)電機+滾珠絲杠”的進給伺服方式已不適應(yīng)這種新要求。而新型的直線伺服驅(qū)動,可以實現(xiàn)直接驅(qū)動,省去了機械變換機構(gòu),提高了進給系統(tǒng)的剛度,降低了傳動環(huán)節(jié)的慣量。于是能提高加工精度和反應(yīng)的快速性,提高了切削速度。因此,直線伺服電動機及其控制技術(shù)便應(yīng)運而生,它可能獲得很高的加、減速度。但是也應(yīng)該看到,在機床上進給系統(tǒng)采用直線伺服電動機實現(xiàn)直接驅(qū)動,雖然獲得了重大好處,但也存在困難和問題。采用直線驅(qū)動之后,系統(tǒng)參數(shù)攝動、端部效應(yīng)、負(fù)載擾動等諸多不確定性因素的影響將直接反映到直線電動機的運動控制中,而沒有任何中間的緩沖過程,因此增加了控制上的困難。這就是說,機械上的簡化導(dǎo)致了電氣控制上的困難,其中包括對傳感器分辨率和反應(yīng)能力要求的提高。此外,還存在著散熱、防磁、防塵等一系列問題。由于直線伺服電動機不可能采用所謂的半閉環(huán)控制方式,只能采用全閉環(huán)控制,系統(tǒng)的任何變化,包括電動機的端部效應(yīng)在內(nèi),切削力的變化對伺服系統(tǒng)來說,都算是干擾,由于沒有減速機構(gòu)的緩沖作用而直接影響到控制器,這會降低性能指標(biāo),甚至導(dǎo)致系統(tǒng)的不穩(wěn)定。所以要設(shè)計出具有強魯棒性的伺服控制器,增加了設(shè)計控制器的復(fù)雜性。
|