機械傳動機構(gòu)設計禁忌機械傳動機構(gòu)具有變速、改變運動形式(旋轉(zhuǎn)運動變?yōu)橹本運動或曲線運動等)、改變運動方式(連續(xù)運動變?yōu)殚g歇運動等)、單向運動變?yōu)橥鶑瓦\動等多種功能。由于其具有結(jié)構(gòu)簡單,性能可靠,不易受電、磁、熱等條件的影響,加工修理方便等優(yōu)點,故得到廣泛應用。如果將機械傳動巧妙合理地應用就可以滿足多種工作要求和性能,所以避免一些常見機械傳動機構(gòu)設計禁忌具有重大的現(xiàn)實意義。 有些機械要求能正反兩個方向轉(zhuǎn)動,設計時應首先考慮采用電動機正反轉(zhuǎn)的方案。對內(nèi)燃機、汽輪機等不能反轉(zhuǎn)的原動機則必須采用在傳動機構(gòu)中設置反向裝置的方案。另外,有些工作機可以空載轉(zhuǎn)動,如機床;有些工作機必須負載起動,如汽車。對其傳動機構(gòu)必須考慮原動機的起動性能,必要時安裝摩擦離合器或液力偶合器,禁忌起動力矩過大,超過了原動機的負載能力。在一般情況下,傳動機構(gòu)中的摩擦傳動在過載時可以打滑,起安全裝置的作用。但是在起重機構(gòu)中,如果重物起吊在高空中,摩擦傳動打滑將引起嚴重的事故。因此,起重傳動機構(gòu)必須有足夠的安全系數(shù),禁忌采用摩擦傳動和安全離合器,如圖2_27所示,圖a較差,圖b較好。
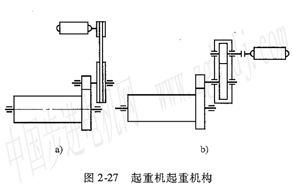 對于要求慢速移動的工作臺,用電動機通過傳動機構(gòu)帶動時,可以采用絲杠螺母副或齒輪齒條傳動機構(gòu),把螺旋運動轉(zhuǎn)變?yōu)橹本運動。但螺旋轉(zhuǎn)動一固工作臺只移動一個螺距而齒輪轉(zhuǎn)一圈齒條移動為πmz(z一齒輪齒數(shù),m一齒輪模數(shù));螺旋每轉(zhuǎn)一圈工作臺移動的距離一般為幾毫米,而齒輪轉(zhuǎn)一圈齒條移動的距離為十幾甚至幾十毫米;當電動機 的轉(zhuǎn)速和工作臺的移動速度相同時,由于螺旋轉(zhuǎn)速可以比齒輪轉(zhuǎn)速高很多,而采用螺旋的傳動比卻比用齒輪的傳動比小得多,所以對于低速移動的工作臺適合采用絲杠螺母副傳動機構(gòu),并且傳動機構(gòu)結(jié)構(gòu)簡單。齒輪齒條傳動適用于移動速度較高的工作臺,如龍門刨床。由此當選擇將旋轉(zhuǎn)運動變?yōu)橹本運動的機構(gòu)時,應注意充分考慮其具體的工作條件和要求,禁忌亂用。 1.齒輪傳動機構(gòu)的設計
由于齒輪傳動具有精度高、轉(zhuǎn)速快等特點,其設計和制造技術(shù)發(fā)展速度較快,齒輪的類型較多,但是在選擇齒輪類型時,應優(yōu)先考慮用圓柱齒輪,直齒和斜齒。圓柱齒輪用于平行軸傳動(按轉(zhuǎn)速高低、平穩(wěn)性要求、是否變速等決定用直齒還是斜齒),直齒錐齒輪用于相交軸傳動,準雙曲面錐齒輪用于交錯軸傳動。設計齒輪傳動機構(gòu)時,必須全面考慮齒輪的強度和硬度、精度、壽命的要求,采用適當可行的加工方法和測量方法,選擇合適的材料和熱處理,潤滑劑和潤滑方法,設計合理的結(jié)構(gòu),以保證質(zhì)量和滿足使用要求。不能滿足質(zhì)量和使用要求的禁忌選用,****不能遷就。以下為進行齒輪傳動機構(gòu)設計時應注意的問題: 1)注意齒輪傳動形式及其傳動比的****匹配選擇。齒輪傳動部件是轉(zhuǎn)矩、轉(zhuǎn)速和轉(zhuǎn)向的變速器。齒輪傳動比i應滿足驅(qū)動部件與負載之間的位移及轉(zhuǎn)速、轉(zhuǎn)矩的匹配要求,用于伺服系統(tǒng)的齒輪減速器是一個力矩變換器,其輸入電動機為高轉(zhuǎn)速、低轉(zhuǎn)矩,而輸出則為低轉(zhuǎn)速、高轉(zhuǎn)矩。因此,不但要求齒輪傳動系統(tǒng)傳遞轉(zhuǎn)矩時要有足夠的剛度,還要求其轉(zhuǎn)動慣量盡量小,以便在獲得同一加速度時所需轉(zhuǎn)速小,即在同一驅(qū)動功率時,其加速度響應為****。此外齒輪的嚙合間隙會造成傳動死區(qū),若該死區(qū)是在封閉系統(tǒng)中,則可能造成系統(tǒng)不穩(wěn)定,常使系統(tǒng)產(chǎn)生以1~5倍間隙而進行的低頻振蕩。為此盡量采用齒側(cè)間隙較小,精度較高的齒輪傳動副。但為了降低制造成本,則多采用各種調(diào)整齒側(cè)間隙的方法來消除或減小嚙合間隙,以提高傳動精度和系統(tǒng)的穩(wěn)定性。由于負載特性和工作條件的不同,****傳動比有不同的選擇方法。在伺服電動機驅(qū)動負載的傳動系統(tǒng)中常采用使負載加速度****的方法。 2)注意各級傳動比的****分配。當計算出傳動比之后,為了使減速系統(tǒng)結(jié)構(gòu)緊湊,滿足動態(tài)性能和提高傳動精度的要求,常常對各級傳動比進行合理分配,其分配原則如下: ①等效轉(zhuǎn)動慣量最小的原則。利用該原則所設計的齒輪傳動系統(tǒng),換算到電動機軸上的等效轉(zhuǎn)動慣量最小。對于伺服傳動系統(tǒng)要求起動、停止和逆轉(zhuǎn)快。當力矩一定時,轉(zhuǎn)動慣量越小,角加速度愈大,運轉(zhuǎn)就越靈敏。這樣可使過渡過程短,響應快,減小起動功率。通過分析計算,可以得出下列結(jié)論:按折算轉(zhuǎn)動慣量最小的原則確定級數(shù)和各級傳動比時,由高速級到低速級,各級傳動比應逐級遞增;而且級數(shù)越多,總折算慣量越小,但是級數(shù)增加到一定數(shù)值后,總折算慣量減小并不顯著,再從結(jié)構(gòu)緊湊、傳動精度和經(jīng)濟性等方面考慮,級數(shù)太多是不合理的。另外還要注意高速軸上的慣量對總折算慣量影響****。 、谳敵鲚S轉(zhuǎn)角誤差最小的原則。為了提高機電一體化系統(tǒng)齒輪傳動系統(tǒng)傳遞運動的精度,各級傳動比應按先小后大原則分配,以便降低齒輪的加工誤差、安裝誤差以及回轉(zhuǎn)誤差對輸出轉(zhuǎn)角精度的影響。在齒輪傳動系統(tǒng)中,傳動比相當于誤差傳遞系數(shù),對傳動精度起縮放作用。因此按傳動精度高的原則分配各級傳動比時,從高速到低速級,各級傳動比也應逐級遞增,尤其最末兩級的傳動比應取大一些,并盡量提高最末一級齒輪副的加工精度。同時應盡量減少級數(shù),從而減少零件數(shù)量和誤差來源。 、垠w積重量最小的原則。對于大功率傳動系統(tǒng),按“先大后小”的原則處理,從高速 級到低速級各級傳動比應遞減,因為高速級傳遞的力矩小、模數(shù)小、傳動比大,體積重量不會大;對于小功率傳動系統(tǒng),因為受力不大,假若各級小齒輪的模數(shù)、齒數(shù)、齒寬相等,各級傳動比應該相等。體積重量常常是精密機械設計的一個重要指標,特別是航天、航空設備上的傳動裝置,應采用體積重量小的原則來分配各級傳動比。 上述三種傳動比分配的原則所反映的規(guī)律不盡相同,在設計中應根據(jù)實際情況的可行性和經(jīng)濟性對轉(zhuǎn)動慣量、結(jié)構(gòu)尺寸和傳動精度提出適當要求。具體來講有以下幾點: a)對于要求體積小、重量輕的齒輪傳動系統(tǒng)可用體積重量最小原則。 b)對于要求運動平穩(wěn)、起停頻繁和動態(tài)性能好的伺服系統(tǒng)的減速齒輪系統(tǒng),可按最小等效轉(zhuǎn)動慣量和總轉(zhuǎn)角誤差最小的原則來處理。對于變負載的傳動齒輪系統(tǒng)的各級傳動比****采用不可約的比數(shù),禁忌同期嚙合以降低噪聲和振動。 c)對于提高傳動精度和減小回程誤差的傳動齒輪系,可按總轉(zhuǎn)角誤差最小原則。對于增速傳動,由于增速時容易破壞傳動齒輪系工作的平穩(wěn)性,應在開始幾級就增速,并且要求每級增速比****大于l:3,以有利于增加輪系剛度、減小傳動誤差。 d)對要求以較大傳動比傳動的齒輪系,往往需要將定軸輪系和行星輪系巧妙結(jié)合為混合輪系。對于要求特大傳動比、并且要求傳動精度與傳動效率高、傳動平穩(wěn)、體積小、重量輕的齒輪系,可選用新型諧波齒輪傳動。 3)注意當齒輪直徑較小或直徑與軸的直徑相近時應做成齒輪軸。 4)注意必要時可以將齒輪的頂圓直徑設計成等于或小于軸的直徑。 5)注意為保證原設計的接觸寬度,忌禁產(chǎn)生階梯磨損,小齒輪的齒寬應稍大于大齒輪的齒寬。 6)注意當齒輪的寬度比較大,而且受力也比較大時,應注意保證沿齒寬齒輪剛度一致,可以采用雙幅板或輻條、加大輪緣厚度的方法,如圖2—28所示,圖a較差,圖b較好。 7)注意對于滲碳/氮淬火和表面淬火的齒輪,要保證齒輪表面硬化層不間斷。 8)注意應禁忌在齒輪與軸的連接時采用錐銷和緊定螺釘?shù)姆椒ǎ驗槠湫瘦^低,可以采用軸向彈簧卡圈的方法,如圖2-29所示,不宜選用圖a、圖b方案,應該采用圖c方案。
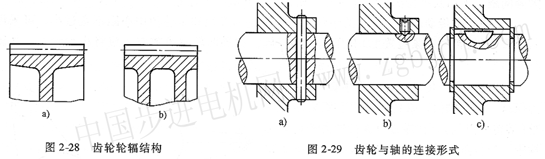 9)注意應提高嚙合機會多的齒輪的硬度。 lO)注意齒輪嚙合時,為避免產(chǎn)生根切、周節(jié)誤差和齒形誤差帶來的影響,應選擇合適的齒數(shù)和速比。 11)安裝齒輪時,應注意齒輪軸的平行度要求,并保證嚙合面給油正確。 12)注意齒輪布置應考慮有利于軸和軸承的受力,****使軸承的載荷方向一定,對于受兩個或更多個力的齒輪,當布置位置不同時,所受的力或疊加或抵消,軸承或軸受力有較 大的不同,設計時應仔細地分析,如圖2130所示,圖a方案不好,圖b方案較好。 13)注意當齒輪的尺寸較大時,常分兩半鑄造,為避免兩半的輪輻結(jié)構(gòu)不合理,剖分面應選擇無輪輻處。 14)注意對于人字齒輪應保證結(jié)合點先進入嚙合,以免擠出的潤滑油產(chǎn)生振動,如圖2-31所示,圖a方案不合理,圖b方案合理。
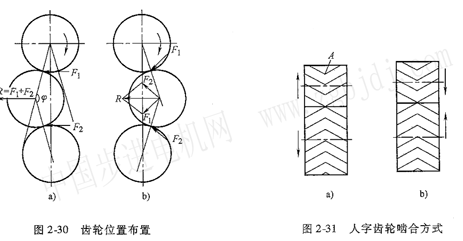 15)注意對于錐齒輪軸必須雙向固定,且大小齒輪都能作軸向調(diào)整,以保證組合錐齒輪結(jié)構(gòu)中的螺栓不受拉力。 2.撓性傳動機構(gòu)的設計
機械中常使用撓性傳動機構(gòu)用于大距離的傳動。撓性元件的彈性較大,可吸收振動,工作平穩(wěn),結(jié)構(gòu)簡單,加工方便。但由于撓性元件的變形較大,以及鏈傳動的多變性效應,帶傳動的彈性滑動等,它的傳動比誤差較大,不易精確傳動。此外,撓性元件磨損較大,壽命較短,必須注意采取適當?shù)木S護措施。在結(jié)構(gòu)設計方面應能方便地更換元件,便于檢查,能及時了解其疲勞和磨損的情況以免發(fā)生事故,還必須禁忌撓性元件由傳動件上脫落和下垂太大等問題。下面幾種情況是設計時必須充分考慮并應格外注意的: 1)注意帶傳動應加大小輪的包角,所以小輪的直徑和帶輪的中心距不宜過小,可采用緊邊置下(鏈傳動中緊邊置上)和壓緊輪等措施,如果兩輪垂直放置,應將小輪置上,如圖2-32所示。
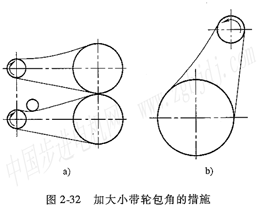 2)注意由于傳動帶在工作中會不斷拉長,為保持一定的拉力,帶傳動的中心距要能夠調(diào)整(鏈傳動也是),在靠自重保持拉力的傳動機構(gòu)中,當自重不夠時要加輔助裝置,如圖2—33所示。 3)注意為防止帶脫落,要保證帶輪軸的平行度和帶輪中心面的平面度的要求;且平帶傳動小帶輪應作成微凸,同步帶輪應考慮安裝擋固,交叉帶不能反轉(zhuǎn)。 4)注意為使帶易交換,帶輪****懸臂安 裝,但是帶過寬時,帶輪應簡支安裝,禁忌沿寬度帶受力不均。 5)注意對于鏈傳動,禁忌用一條鏈條帶動一條水平線上的多個鏈輪。 6)鏈條運動方向要與卡簧的方向適應,禁忌產(chǎn)生沖擊、跳動、脫落,如圖2.34所示,且鏈條定期潤滑。
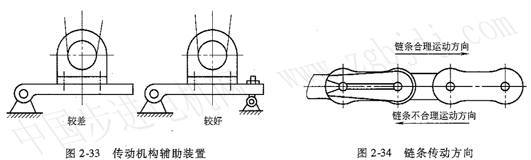 7)為了保證繩的壽命,繩輪的直徑禁忌任意減;對于鋼繩禁忌任意彎曲,且鋼繩定期潤滑。 8)注意撓性傳動拉力變動對軸承負荷的影響。 3.間歇傳動機構(gòu)的設計
用間歇傳動機構(gòu)時,應考慮機構(gòu)的運動系數(shù),系數(shù)應盡可能地減小,以提高其工作效率。對于凸輪間歇機構(gòu),還要注意移動從動件與偏置凸輪的位置,以使壓力角較小,運動靈活,如圖2—35所示,禁忌圖a方案,應選用合理的圖b方案。
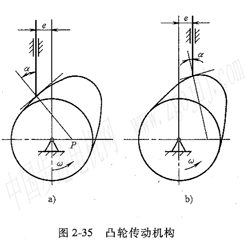 4.大傳動比機構(gòu)的設計
注意對于要求傳動比大而且對其工作位置有一定要求的傳動機構(gòu),往往傳動級數(shù)較多,結(jié)構(gòu)比較復雜,如果采用絲杠螺母傳動、齒輪傳動、撓性傳動作為散件安裝,存在精度不高、缺乏潤滑、安裝困難、壽命較短等缺點,所以常采用大傳動比的標準減速器代替散裝的傳動機構(gòu)就是很好的方案,目前已有把電動機和減速器作為一個整體的減速電動機,作為一個標準件供應,這樣既簡化了結(jié)構(gòu),又減少了支撐件的受力,節(jié)省了占地面積。 注意對于大多數(shù)的機械傳動機構(gòu),電動機、減速器、工作機各用螺栓固定在地基或機架上。各部分之間用聯(lián)軸器連接,這些聯(lián)軸器一般都用撓性的,即對其對中要求較低。但是為了提高傳動效率,減小磨損和聯(lián)軸器不對中產(chǎn)生的附加力,在安裝時還是盡量提高對中精度,這就使安裝工作繁重。如果改用軸裝式減速器,用帶傳動連接電動機和減速器,就避免了安裝聯(lián)軸器的麻煩。
|